Chapter I Preparation basis and preparation instructions
First, the basis for preparation:
Current national construction and installation engineering construction and acceptance specifications (procedures), quality inspection and evaluation standards;
Compulsory Provisions for Engineering Construction Standards;
"Uniform Standard for Construction Quality Acceptance of Construction Engineering" (GB 50300);
Technical Specifications for Roofing Engineering (GB 50345);
"Code for Quality Acceptance of Roofing Projects" (GB 50207);
"Uniform Standard for Construction Quality Acceptance of Building Engineering" GB 50300
"Technical Specifications for Roofing Engineering" GB 50345
"Technical Specifications for Underground Engineering Waterproofing" GB 50108
"Code for quality acceptance of roofing works" GB 50207
"Code for Quality Acceptance of Underground Waterproof Engineering" GB 50208
General Rules for the Design of Civil Buildings GB 50352
"Technical Regulations for Building Indoor Waterproofing Engineering" CECS196:2006
"Code for Design of Corrosion Protection for Industrial Buildings" GB 50046
Technical Regulations for Planting Roofing Engineering JGJ 155
"Code for Construction and Acceptance of Building Anti-corrosion Engineering" GB 50212
Polymer Cement Waterproof Coating GB/T 23445
"polymer cement waterproofing paste" JC/T 2090
"Uniform Standard for Construction Quality Acceptance of Building Engineering" GB 50300
"Technical Specifications for Roofing Engineering" GB 50345
"Technical Specifications for Underground Engineering Waterproofing" GB 50108
"Code for quality acceptance of roofing works" GB 50207
"Code for Quality Acceptance of Underground Waterproof Engineering" GB 50208
General Rules for the Design of Civil Buildings GB 50352
"Technical Regulations for Building Indoor Waterproofing Engineering" CECS196:2006
"Code for Design of Corrosion Protection for Industrial Buildings" GB 50046
Technical Regulations for Planting Roofing Engineering JGJ 155
"Code for Construction and Acceptance of Building Anti-corrosion Engineering" GB 50212
Polymer Cement Waterproof Coating GB/T 23445
"polymer cement waterproofing paste" JC/T 2090
General Rules for the Design of Civil Buildings GB 50352
"Technical Regulations for Building Indoor Waterproofing Engineering" CECS196
Technical Regulations for Planting Roofing Engineering JGJ 155
Polymer Cement Waterproof Coating GB/T 23445
"polymer cement waterproofing paste" JC/T 2090
"Pre-ply, wet-laid waterproofing membrane" GB23457
"bearing waterproof membrane" GB/T 21897 "cement-based permeable crystalline waterproof coating" GB 18445
Technical Specification for Lightweight Aggregate Concrete Structure (JGJ 12)
Relevant drawings, engineering features, construction site environment and natural conditions of the project.
Second, the preparation instructions:
This design and construction plan is applicable to the roofing and bathroom waterproofing project of Yulong Garden Phase 2 project.
The “Project” below refers to the construction content included in this waterproof project.
Chapter II Project Overview and Features
I. Project Overview
The existing roof and bathroom parts of the project are planned to be waterproof. According to the actual site survey of our company, the waterproof construction plan of this project is specially prepared for the owner, design, general contractor, supervision and related personnel.
a), Building 6: Floor tile floor (with waterproof layer) waterproofing practices:
1. Floor tile layer 2.2 thick modified MD polymer waterproof layer 3.20 thick 1:3 waterproof mortar (plus 5% waterproofing agent) defects flattened, and turned 30CM along the corner of the wall 4. Reinforced slab
2) The roof is divided into house 1: insulated roof, house 2: non-slip floor tile roof, house 3: planting roofing practices:
1. House 1: Insulated roof: 1.40 thick C20 fine stone reinforcement 砼 2.2 thick YYPE redundant waterproof bonding material + 1.2 thick PAWM-3 redundant waterproof coil 3.50 thick (the thinnest part) ceramsite concrete redundant layer Find 2% slope (waterproof and heat insulation to find the slope leveling) 4. Reinforced slab roof panel
2, House 2: Non-slip floor tile roof: 1. Anti-slip floor tile 2.2 thick YYPE redundant waterproof bonding material +1.2 thick PAWM-3 redundant waterproof coil material 3.50 thick (the thinnest part) ceramsite concrete redundant layer to find 2% slope (waterproof and heat insulation to find the slope leveling) 4. Reinforced slab roof panel
3, planting roof (top to top): 1. ceramsite planting soil 2. geotextile cloth 3.15 thick concave and convex row (storage) water board + ceramsite water filter layer 4.2 thick YYPE redundant waterproof bonding material +1.2 thick PAWM -3 redundant waterproof coil 5.50 thick (the thinnest part) ceramsite concrete redundant layer to find 2% slope (waterproof and heat insulation to find the slope leveling) 6. Reinforced slab roof panel
Second, the construction objectives:
1) Quality objectives:
a. The quality of the project meets the nationally stipulated eligibility criteria.
b. The quality of the project meets the design requirements and the standards stipulated in the contract.
c. “Code for Quality Acceptance of Roofing Engineering” (GB 50207).
d. Specification for quality acceptance of building interior bathroom waterproofing engineering.
2) Duration target:
Our company will meet the requirements of the owner and the general contractor, concentrate manpower, financial resources and material resources to ensure that the construction period is not delayed, complete the construction task under normal construction conditions, and never affect the overall progress of the project due to the lag of the waterproof project.
3) Safety objectives:
Prevent serious injuries, eliminate deaths, and meet the "four no" requirements of no major casualties, no major mechanical accidents, no fire accidents, no food poisoning accidents.
Chapter III Project Management Framework
In order to better complete the construction of this waterproof project, our company set up a “waterproof project manager department” at the construction site, equipped with the corresponding project management team, and implemented project management for the project. The project management team and the construction operation layer of the project department are equipped with department heads with rich experience and high technical level, and the project manager is responsible for the whole project.
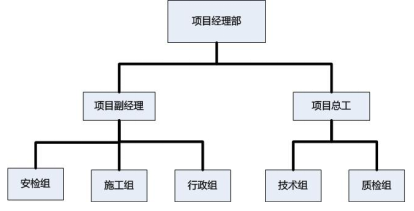
Division of management responsibilities:
Duties
Project manager
Project Deputy Manager Responsible for specific work arrangements
Project manager, construction management, organization, coordination, etc.
Quality inspection team, security inspection team, responsible for on-site quality and safety
Construction team responsible for construction implementation
Technical team responsible for construction technical support
Administrative team is responsible for security and warehouse management
Chapter IV Technical Support
First, material monitoring and inspection:
1. The performance indicators of the applied waterproof materials are in accordance with the standards listed in the product specification and meet the corresponding national or industry standards. Some of the featured products that have not yet been produced by the corresponding countries or industries have implemented corporate standards. The materials entering the site will be sampled by your company and sent to the testing agency for inspection. If there are any unqualified products, our company will bear the corresponding responsibility.
2. The materials provided are all accompanied by the product certificate label and the factory inspection report. Your company can check the production date and the delivery site of the batch according to the certificate label or the QR code to distinguish the authenticity.
Second, technical staff training:
1. Organize the training of cargo storage so that all users, especially the waterproof material storage personnel, understand the requirements for storage and storage of waterproof materials, so that the materials can be smoothly applied to the project.
2. Organize on-site technical disclosure, detailing specific construction practices and operating procedures, precautions, and quality requirements.
3. Carry out on-site operation training for the construction team, so that it can be seen from the material to the machine, to the whole process of operation and acceptance.
4. Give timely and accurate answers to the problems concerning the use of waterproof materials and engineering construction.
Third, the construction process guidance:
1. Grasp the supply and construction process as a whole.
2. Provide a comprehensive construction site service for the waterproof construction team to help solve various problems encountered during the construction, so as to facilitate the smooth progress of the project.
3. Provide key technical support for key parts and key time slots, and provide 24-hour uninterrupted on-site service when necessary to ensure project quality.
4. Supervise the construction of the project at any time during the construction process and find that the practices that do not meet the specifications, procedures and construction plans are immediately corrected.
5. Assist in construction inspection and preparation of inspection and acceptance materials.
Fourth, quality inspection:
1. Strictly implement the inspection system for each material, strengthen the quality inspection of the incoming materials and the inspection of the construction process. All materials must be notified of the inspection before they can be used.
2. During the construction process, the company arranges special personnel to inspect and supervise the construction quality, and provides inspection records for Party A to check and record.
Fifth, timely feedback of information:
Establish a reasonable project manager team, summarize and discuss the problems that arise in the project, and solve the problems on the day. If you need the owner and the general contractor to help, communicate with the owner and the general contract within 24 hours.
Chapter V Construction Resources Investment Plan and Guarantee Measures
First, equipment entry plan
The mechanical equipment configuration is detailed in the attached table. Because the waterproof construction uses less mechanical equipment and small size, it does not occupy the construction area, and the mechanical equipment comes into the field with the construction workers.
Second, the material entry plan
According to the construction schedule plan, timely purchase, so as to meet the construction requirements, but also to make the site without too much backlog, so that there are more venues to arrange construction. Establish an effective material market survey and procurement and supply department.
Third, the labor arrangement plan and construction schedule
According to the actual situation of the project, our company plans to deploy a professional construction team, arrange the construction period according to the overall progress of the project, and if necessary, adjust the personnel within the company to increase the manpower to ensure the progress of the project.
Fourth, the main construction machinery and equipment
Main construction machinery and equipment table
No. Type Number Remarks
1 Bucket 6 vehicles for horizontal transportation of waterproof materials
2 spraying equipment 6 sets of spray waterproof coating
3 waterproof coating mixer 6 sets of mixing waterproof coating
4 Ash shovel, brush, bucket Several for cleaning the base layer, charging, node processing
5 air compressor, high pressure cleaner 2 sets of spray, water spray, dust washing
V. Guarantee measures
1. Funds guarantee measures: Prepare sufficient liquidity, allocate funds to labor expenses, materials and other aspects, and do not misappropriate project funds to ensure the funds are earmarked for the construction.
2. Formulate plans and use plans.
Chapter VI Engineering Design and Construction Plan and Technical Measures Requirements
Within the reasonable life of the building, it is water-tight, able to withstand the influence of nature, environment and use on the building, and the building is protected from water erosion is an essential element. At the same time, waterproofing should also protect and reinforce the building itself, meet the requirements of economical and environmental pollution. Building waterproofing design, materials, construction and maintenance as a systematic project plays an important role in the use of buildings. The quality of the waterproof project depends on the selection of the waterproof material and its associated application technology.
Construction application product introduction
First, modified MD polymer waterproof coating (type III)
The design and construction of this project are intended to be applied to the floor and side wall of the project floor 6: floor tiles (bathroom, kitchen room).
Building waterproof coatings are divided into two categories: oil-based coatings and water-based coatings. The oily coatings are mainly polyurethane waterproof coatings and polyurea waterproof coatings. The coatings of oily coatings have excellent water resistance, but contain a large amount of organic solvents, are flammable at the construction site, and are harmful to human health, and are increasingly difficult to promote in reality. Water-based paints are mainly organic polymer emulsion waterproof coatings, non-toxic, non-flammable, and more and more popular with construction workers, but their coating film water resistance is far less than oily coatings, in the case of long-term water immersion, the coating film is easy to swell, Therefore, the waterproof performance is gradually lost. Therefore, improving the water resistance of the water-based paint has become a problem that the waterproof industry is trying to solve.
In addition to taking into account other properties of water-based paints, in order to improve the water resistance of water-based paint coatings, we mainly work from the following aspects:
(1) Select a polymer emulsion with good water resistance. Finally, a polymer emulsion with a polyacrylate emulsion as the main component was selected, and the polymer emulsion supplier was finally determined by comparing the water resistance and other properties of the polyacrylate emulsion coating film produced by different companies;
(2) Select a filler with good water resistance. Gradually discarding the inert filler, giving up the production of one-component polymer emulsion waterproof coating, selecting cement that can participate in the curing reaction as a filler to produce a two-component water-based waterproof coating;
(3) Select the blending ratio of cement. The polymer emulsion is mixed with cement. As the proportion of cement increases, the water resistance of the coating film becomes stronger and the flexibility becomes worse and worse, thereby producing polymer cement waterproof coatings type I, type II and type III products and polymerization. Cement waterproofing paste type I and type II products, and finally transition to polymer waterproof mortar. In this process, the waterproof coating gradually transitions from the cement modified polymer to the polymer modified cement, from the initial polymer as the continuous phase, the cement as the dispersed phase to the cement as the continuous phase, and the polymer as the dispersed phase. .
1 Technical characteristics
The modified MD polymer waterproof coating produced by Zhengzhou Sainuo Building Materials Co., Ltd. is a two-component material. The component A is a polyacrylate emulsion and a silicone waterproofing agent, and the component B is cement, quartz powder, calcium oxide powder and nitrous acid. Sodium modifier, etc.
The modified MD polymer waterproof coating has three technical features:
(1) Forming a flexible waterproof coating film with good water resistance on the surface of the base layer.
First, the component A selected a polyacrylate waterproof emulsion with good water resistance;
Secondly, the hydrophobic agent added to the emulsion can reduce the water absorption rate of the coating film, thereby improving the water resistance of the coating film;
Third, the coating film with cement as a filler is beneficial to improve the water resistance of the coating film;
Fourth, the product implements the technical requirements of Type III products in GB/T 23445-2009 "Polymer Cement Waterproof Coatings", the tensile strength of the coating film is not less than 1.8 M Pa, and the elongation at break is not less than 30%.
Through the above four measures, the modified MD waterproof coating forms a flexible waterproof coating film with better water resistance on the surface of the base layer.
(2) Form a rigid waterproof layer on the concrete surface.
The hydrophobic additives and other modified materials added in the coating can penetrate into the concrete base layer by 0.5~1.0 mm deep, improve the compactness of the concrete surface layer, and impart hydrophobic properties to the concrete surface layer, forming a rigid waterproof layer.
(3) Automatic healing properties of concrete cracks.
According to GB 18445—2012 “cement-based permeable crystalline waterproof material”, the performance test shows that the product can make the concrete base layer have secondary impermeability, indicating that the product can automatically heal the micropores of concrete.
1.1 Waterproof mechanism
When used, the mixture is uniformly mixed in a ratio of (component A); (component B) = 1.0; 1.0, and the mixture is coated on the substrate. The water in the emulsion has three destinations: (1) volatilization into the air; (2) chemical reaction with the cement; and (3) infiltration into the substrate. As the moisture disappears, the mixture forms a flexible waterproof coating on the surface of the substrate. Some hydrophobic additives remain in the coating film, chemically react with carbon dioxide in the air and moisture in the mixture to form an alkane. A new substance based on a silanol group, which is rapidly polymerized by its own silanol to form a hydrophobic polysiloxane, thereby improving the water resistance of the coating film.
The water that penetrates into the base layer carries the water-soluble modifier in the product (there are several modifiers, among which there are hydrophobic agents with reactive groups). After the hydrophobic agent penetrates into the pores of the base layer, it chemically reacts with water, carbon dioxide gas and carbonate ions in the base layer to form a new substance with an alkyl group and a silanol group. The silanol groups in the new substance are polymerized by themselves and The hydroxyl group in the concrete surface polymerizes to form a water-insoluble and hydrophobic polysiloxane on the inner surface of the capillary. In this process, the water-absorbing hydroxyl group disappears, and the hydrophobic alkyl group is distributed on the inner surface of the concrete without pores. (See Figure 1), which improves the compactness of the concrete and imparts hydrophobic properties to the surface of the substrate and the inner surface of the capillary. Due to the chemical bond between the silicone and the concrete base layer, it can be firmly bonded to the concrete base. Therefore, MD modified polymer waterproof coating forms two waterproof layers: (1) polymer cement flexible waterproof coating; (2) concrete base surface rigid waterproof layer.
Figure 1 Schematic distribution of polysiloxane in concrete micropores
Product performance
In April 2017, Henan Jianshe Building Materials Testing Co., Ltd. tested the modified MD polymer waterproof coating according to GB/T 23445-2009 and GB 18445-2012. The product performance is shown in Table 1. The test report shows that the product not only meets the technical requirements of Type III products in GB/T 23445-2009, but also the secondary impermeability index shows that the modifier in the product can make the concrete crack have an automatic healing function.
Performance index of modified MD polymer waterproof coating (type III)
In the product performance test conducted by Zhengzhou Sainuo Building Materials Co., Ltd., the waterproof coating on the surface of the test piece was peeled off, and water was dripped on the surface of the base layer, indicating that the surface of the test piece had hydrophobic properties (see Figure 2). The test piece was broken and immersed in water. It was observed that the surface layer of the test piece with a thickness of 0.5 to 1.0 mm did not absorb water and was in a dry state, while other parts of the test piece were completely wetted by water.
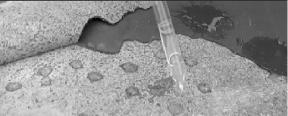
Figure 2 Hydrophobic performance of the test block surface
2 Operating points
2.1 Grassroots requirements
The modified MD polymer waterproof coating is suitable for concrete, mortar and masonry base layers, and the base layer is required to be firm, smooth, clean and free of clear water. The loose layer, the steel head and the ash on the surface of the base layer should be removed, and construction tools such as steel brushes, polishing machines, chisels and hammers can be used. The holes and grooves on the surface of the base layer shall be smoothed with cement mortar mixed with the A component of this product. Through the basic treatment measures, a flat, strong base layer is obtained. The surface of the base layer is flat and it is easy to control the uniformity of the thickness of the coating. The surface of the base layer is strong, which is beneficial to improve the bond strength between the coating and the base layer.
Although the product can be applied on a wet substrate, the dry base layer is more conducive to water carrying the active group-containing modifier into the interior of the substrate, which is beneficial to form a thicker rigid waterproof layer.
2.2 Environmental requirements
The modified MD polymer waterproof coating is similar to the environmental conditions required for the construction of most (JS) polymer cement waterproof coatings. When applying this product, the ambient temperature should be 5~400C, and should not be constructed in high humidity environment and rainy days. When the temperature is lower than 0 0C, the coating icing can not form a film; when the temperature is 0~50C, it is not conducive to the evaporation of water in the coating; when the temperature is higher than 400C, the surface of the mixture quickly loses water and conjunctiva, and the internal moisture is blocked. It is easy to cause the film to bulge; in a high humidity environment, it is not conducive to the evaporation of water into the air, and the coating film is difficult to form; in the rain, when the coating is not formed, the mixture is washed away by the rain. When using the spraying process, it is not allowed to be constructed when the wind is above 5 or higher, so as to prevent the mixture from being blown around.
2.3 Construction process
The coated modified MD polymer waterproof coating can be applied by a doctor blade method or a spray coating method, and a multi-pass survival process is adopted. After the coating is applied on the base layer, the water will form micropores on the coating film during the evaporation to the atmosphere, which will affect the water impermeability of the coating film. When the multi-pass activation process is used, the coating applied in the second pass can be closed. The micropores on the first coating, the coating applied in the third coating can close the micropores on the second coating film, and so on, through multiple coatings, a certain thickness of the impervious waterproof coating is finally obtained. .
2.3.1 Detail processing
In the easily deformed base layer such as tube root, yin and yang angle, and divisional joint, a two-coat construction process is adopted, and the carcass is added to the additional joint portion to enhance the additional layer, and the carcass material can be mesh cloth. Carcass reinforcement is used in the deformable part to prevent the coating from exhibiting zero elongation fracture. It is difficult for any highly extensible coating to resist the fine cracking of the base layer. When the base layer is slightly cracked, the coating adhered to its surface is infinitely stretched. Since any coating is unlikely to have an infinite stretch, the coating must be destroyed when the base layer is cracked. When the coating contains carcass reinforcing material, when the base layer is cracked, the coating under the carcass is pulled off from the base layer, and the coating on the carcass is intact, thereby ensuring the integrity of the coating film.
2.3.2 Large area coating
At the engineering site, the base layer will also be cracked outside the detail node. The location of the cracking is unpredictable. In order to prevent the coating from causing zero elongation fracture, the carcass reinforcement material should be laid first by a coating process, and then the large-area coating is started. cloth.
Put the component A into the mixing tank, slowly add the component B with a hand-held electric mixer, and control (component A); (component B) = 1.0; 1.0, stir evenly to form a mixture. material. Using a one-coating process, the carcass reinforcement layer is laid with the mixture, and then the mixture is evenly sprayed on the surface of the carcass reinforcement layer by spraying equipment. The mixture can also be evenly squeegeed with a squeegee, a brush or a roller brush. Scrape on the surface of the carcass reinforcement layer. The first coating is applied to the film and coated for the second time, and coated 2 to 3 times to form a dense waterproof coating of the designed thickness.
The mixture should be used up within 30 minutes. When the mixture thickens, stir the mixture.
Second, PAWM-3 redundant waterproof membrane sealing system
The design and construction of this project are intended to be applied to this project: house 1, house 2, house 3 roof waterproof seal.
It is made up of a new generation of modified polymer waterproof sheet and double-sided (PAWM-3) polymer long fiber, which is introduced into the reliability theory of modern design method, and is constructed with high-performance YYPE redundant waterproof bonding material. Redundant, high-density, high-impedance, high-reliability redundant sealing and waterproofing system, YYPE redundant waterproof bonding layer and anti-environmental protection layer have self-healing function, which is formed after the concrete layer is fused and consolidated. Waterproof bonding layer, combined with the gaplessness of concrete and waterproof coiled material, enhances the self-waterproof function of concrete, eliminates hidden dangers between water-repellent layers, forms a layer of construction, multiple waterproof redundant sealing waterproof system, waterproof of the waterproof system The layer is not easily damaged, and it is not easy to leak even if it is damaged, and the sealing is reliable. According to Sino's redundant sealing theory, even if the waterproof layer is seriously damaged in the later stage, it will cause partial water leakage. Because of the existence of the redundant system, it will not cause large-scale drowning, and the maintenance is very convenient and simple. Enterprise production standard: Q/ZZSN 01-2016
Construction features:
1. The waterproof layer is greatly reduced by the influence of the settlement of the main structure;
2, no need to level the floor, can be constructed on the surface of the water and wet;
3. The reinforced concrete can be poured without the need of a coil protection layer.
Features
1. It has high toughness: it has anti-puncture self-healing performance, high elongation, high tensile strength and tear strength, and effectively prevents plant root puncture;
2, strong bonding: good bonding and sealing performance, effectively prevent drowning;
3. Chemical corrosion resistance: excellent resistance to acid and alkali salts and other chemical media;
4, UV resistance, high temperature resistance, aging resistance, long service life, and the product is non-toxic and tasteless, in line with environmental protection requirements;
5, high waterproof reliability, a variety of high-performance materials to form a redundant waterproof system with multiple waterproof effects, not easy to be destroyed during construction, is also not easy to leak water, and will not drown;
6. Simple and convenient construction, low process requirements and cost savings.
Testing technical indicators "bearing waterproofing membrane" GB/T 21897-2008
Application field
1. It is suitable for waterproofing of floor and flat roofs of industrial and civil buildings, roofs of upper floors, non-superior roofs, green roofs, water storage roofs, roof gardens, etc.;
2. It can be used in places with acid, alkali or drugs to prevent corrosion, anti-virus and anti-seepage projects; it is suitable for roofs with vibration or large settlement of base structure;
3. Suitable for underground projects such as basements, underground garages, civil air defense projects, subways, tunnels, cable trenches, pipe corridors, underground continuous walls, and waterproofing and seepage prevention for sewage pools, clear water pools, bridges, reservoirs, canals, military facilities, etc. , moisture-proof works.
4 construction methods
The waterproof system has no open flame during construction, no harmful gas, no need for heating, and the construction is carried out by wet paving or pre-packing anti-sticking method during construction, and the construction is simple and the speed is fast.
Third, YYPE redundant waterproof bonding material
The design and construction of this project are intended to be applied to this project: house 1, house 2, house 3 roof waterproofing, bonding PAWM-3 redundant waterproofing membrane.
Sino technology always strives for the best, and thinks about the worst. The developed YYPE redundant waterproof adhesive has lower requirements on the site, so the reliability of the waterproof system is easy to achieve, even the worst. When it happens, it will not cause the system to crash, which greatly improves the quality of the project.
Performance characteristics:
1. The bonded coil is used as a waterproof layer.
2. The adhesive layer of 1-2 mm thickness is the second waterproof layer.
3. The binder penetrates into the concrete to close the capillary pores to form a third waterproof layer. The product produces crystals of two states in the capillary pores inside the concrete: hydrophilic and hygroscopic, and the crystal can seal the cavity inside the concrete. , blocking moisture infiltration from both positive and negative directions.
4. Even if the first and second waterproof layers are damaged, the third waterproof layer will function and still will not leak.
5, even if the third layer is destroyed, water leakage occurs, but it will never drown, has a "self-healing" function, basically no maintenance.
6. Combining the above reasons, after using YYPE redundant waterproof bonding material, the safety and reliability of waterproof construction is greatly improved, which greatly reduces the probability of the overall collapse of the waterproof system, and the waterproof durability is guaranteed.
Construction method:
1. Put the YYPE redundant waterproof bonding material into the mixing tank, add water (powder and water according to 1:0.2-0.25) and stir for 3-6 minutes to form a uniform paste. Allow to stand for 10 minutes to fully mature. Before the construction, the slurry can be further stirred for 1 minute, and the construction methods such as scraping, painting, spraying, and sweeping can be used. The mixed slurry must be used up within 2 hours.
2, the base layer treatment: first clean the base layer, reveal a strong base surface, and keep wet. Note: The base layer must not have floating dust, oil stains, and loose materials to affect the bonding.
3, the corner should be done in a circular arc shape, to strengthen.
4. No need for maintenance.
Fourth, redundant ceramsite concrete
The design and construction of this project are intended to be applied to this project: house 1, house 2, house 3 roof insulation, waterproof, slope finding, leveling integration construction.
The ceramsite is used instead of the stone as the coarse aggregate of the concrete, and the redundant waterproofing agent is added. The prepared concrete is called “redundant ceramsite concrete”. It can be used as a waterproof and thermal insulation for roofing to find integrated construction materials for slopes.
Chinese name: Redundant ceramsite concrete
English name: Redundancy Ceramisite Concrete
Bulk density: no more than 1900kg/m3
It is made from cementitious materials and lightweight aggregates.
According to the use, it can be divided into heat preservation: density is 800kg/m3 or less; structural heat preservation: density is 800~1400kg/m3; structure: density is 1400kg/m3 or more.
Can be divided into all-light concrete (with light sand) and sand light concrete (with ordinary sand).
use:
Lightweight aggregate concrete has better heat and fire resistance than ordinary concrete, but its modulus of elasticity is lower.
Lightweight aggregate concrete with ceramsite as coarse aggregate and ordinary sand or ceramic sand as fine aggregate is called ceramsite concrete.
The strength of the ceramsite concrete for structure can be greater than 40 MPa, and the heat preservation and heat resistance are good.
Can be used in building construction, bridges, boats and kiln foundations. Ceramsite concrete, commonly known as “lightweight crucible”, solves the problem of small selection of dry density of ordinary crucibles, which makes the selection of dry density of concrete more perfect.
Density level
The density grade of ceramsite light concrete is divided into 800, 900; 1000; ...; 1800; 1900 (KG/M3).
Five, YYM infiltration crystal waterproofing agent
The design and construction of this project are intended to be applied to this project: house 1, house 2, house 3 roof insulation, waterproof, slope finding, leveling integrated redundant ceramsite concrete waterproofing admixture.
1 Product Introduction
YYM high performance penetrating waterproofing agent (type I: powder) is a new environmentally-friendly and efficient permeable crystalline concrete admixture.
Type I is a gray inorganic powder. Concrete, mortar and water added with YYM waterproofing agent react with cement to produce multiple active substances, which make concrete and mortar have self-healing waterproof function and provide protection for concrete reinforcement to form a complete sealing layer. To avoid the infiltration of water and have a destructive effect on concrete and mortar.
2 Product implementation standards
Type I implementation standard: JC 474-2008
3 product specifications, code, trademark
Specifications: Single component, packed in sealed plastic drums, weighing 20 kg per barrel.
Code: YYM
Trademark: Yuyan
4 Product Features
1). Durable; self-healing 400 micron small static crack;
2). Improve the strength;
3) Protect the steel bars from corrosion;
4). Water pressure resistance up to 14 bar;
5). No need to make waterproof layer;
6). The amount of addition is small, type I: 2% of the weight of the cement;
5 Scope of application
1. used for water storage structure; drinking pool, sewage treatment plant, septic tank;
2. For waterproof structure: tunnel, elevator foundation pit, dam body;
3. Underground engineering: building foundation;
4. Mass concrete;
5. Brick wall, stone base.
The first part of the indoor (bathroom, kitchen room) waterproof project
First, indoor (bathroom, kitchen room) waterproof engineering materials
The indoor bathroom has small kitchen area, many wall and hole holes, many yin and yang corners, many kitchen equipments, and complicated connection with the ground, floor and wall. The waterproof material used should be able to adapt to changes in the shape of the base layer and facilitate the change. The laying of pipeline equipment is not affected by the shape of the base layer, and the water impermeability is good. It is advisable to use a waterproof coating with no joints and good integrity. Therefore, the following requirements should be met when purchasing waterproof materials in the toilet room:
(1) Waterproof coatings have good water resistance, and the waterproof performance does not decrease even under long-term water immersion conditions.
(2) Good overall, effectively preventing production water, domestic wastewater, and sewage from infiltrating into walls, floors, or downstairs.
(3) Within a reasonable period of use, the film is adapted to structural deformation and will not cause leakage.
Second, waterproof coating waterproof layer design
Building 6: Floor Tile Floor Kitchen, Bathroom Side, floor waterproof:
Node Enhanced Additional Layer + 1.2 Thick Modified MD Polymer Waterproof Coating (Type III)
Third, the main characteristics of modified MD polymer waterproof coating
Two-component, semi-rigid, semi-flexible, one-time construction, multiple waterproof, strong adhesion, long-term water-resistant soaking. Subsequent construction is not easily damaged, and even if it is damaged, it is not easy to leak water, effectively improving waterproof reliability.
Construction method: sprayable, brushable, scratchable, and coatable.
Applicable base: concrete, brick wall, mortar layer, base layer dry and wet can be constructed.
Scope of application: waterproof in kitchen, bathroom, terrace, pool, etc.
Efficient, non-toxic, harmless and non-polluting, can be used in drinking water tanks and other projects.
It can be directly applied to the wet or dry substrate.
Fourth, the key points of modified MD polymer waterproof coating construction
a), working conditions
1. The waterproof construction unit shall have the corresponding construction qualification for the national building waterproof engineering.
2, waterproof workers through waterproof professional training.
3. The grassroots level meets the design and specification requirements. Before the construction of the waterproof project begins, the quality of the previous process should be checked and accepted before construction.
4. All kinds of pre-embedded pipe fittings should be pre-buried in advance according to the design and specification requirements, and waterproof sealing treatment should be done.
2) Construction preparation
1) Material preparation
Modified MD polymer waterproof coating (type III) liquid and powder.
2) Construction equipment
A. Tank: It is advisable to choose a round bottom container made of plastic or iron.
B. Small paint bucket: used for charging.
C, long hair roller, brown hair brush: used to paint.
D, small iron scraper: used to apply scraping mixture in complex parts.
E, paint brush, round brush: used to paint the primer.
F, small trowel: used to repair the grass.
G, oil shovel, shovel, rag, high pressure hair dryer: used to clean the grass.
c), construction process
1, grassroots processing
(1) There is a small depression for the base layer, and it can be flattened with 1:2.5 cement mortar.
(2) The base layer requires flatness and no sharp objects. If the base layer irregularities do not meet the construction requirements, the uneven base layer chisel is cleaned and then repaired with cement mortar to make the base layer meet the construction requirements.
(3) Reinforcement treatment of complex parts: firstly apply waterproof coating to enhance the complex parts such as yin and yang angles and pipe roots, and reinforced with glass fiber mesh cloth. The reinforcing material should be close to the base layer, and there should be no defects such as empty drums, wrinkles, and ridges. The surface should be coated with a layer of paint to naturally cure.
2, operating points
(1) In order to ensure that the thickness of the waterproof layer meets the specified requirements and ensure that the thickness is uniform, the base surface is fully wetted first, and should be layered and applied, and each pass should not be too thick. On the planar base layer, the waterproof coating is generally applied twice, and the amount of coating per coating is about 1.3 kg/m2; the film formation is about 1.2 thick. On the base of the façade, it is generally applied 3 times. In order to avoid the flow of the waterproof coating, the amount of coating per coating is about 0.7 kg/m2. The film formation is about 1 thick.
(2) After the first coating is applied, when the coating is substantially cured until it is not sticky, the second coating is performed. The coating of the third coating is applied according to this requirement. The coating for each adjacent two passes should be applied vertically to ensure uniform film thickness and to seal capillary pores in any part of the substrate.
(3) The curing time of each coating should be about 1-2h in summer; in winter, measures should be taken to ensure film formation within 24h.
(4) If the design requires carcass reinforcement at the coating joint, the carcass material should be applied to the flat part while applying the second coat; the opposite part should be coated with the third coat. Attach the carcass material. It should be ensured that it is flat, free from air bubbles, empty drums, and pleats. When coating the coating on the carcass, the coating should be completely covered with the carcass, and there should be no external dew exposure.
(5) Coating and interval time control: Coating thickness is a key issue affecting the waterproof quality of the film, but it is difficult to accurately control the thickness of the coating by hand. Because each coating should be painted several times before painting, and the coating film should not be too thick. If it is too thick, the surface of the coating film will be dried to form a film, but the moisture or solvent of the internal coating will not evaporate. Or the phenomenon of volatilization makes the coating film difficult to dry and does not form a waterproof film with a certain strength and waterproof ability.
(6) The coating time interval can be applied to the next coating film by touching the coating film without sticking hands.
3. Construction sequence
The construction sequence of the water-repellent coating for waterproofing of the coating film should follow the principle of “first, then, then high, then low, first fine, large front, and front façade” to facilitate film quality and film protection. Special parts such as additional layers of yin and yang should be painted first, and then a large area should be applied after the requirements are met. During the operation, the evenly mixed paint is poured on the base layer, and the material is scraped flat with a squeegee, and the layers are longitudinally and horizontally coated, and after solidification, a waterproof film which is seamless and firmly bonded to the base layer is formed. Facade painting height: The height of the bathroom with shower requirements should not be less than 1.8 meters; for toilets without showers, the height should not be less than 0.3 meters.
Five, indoor (toilet) waterproof structure
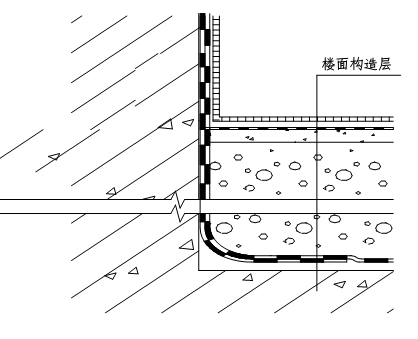
Sunken bathroom corner structure
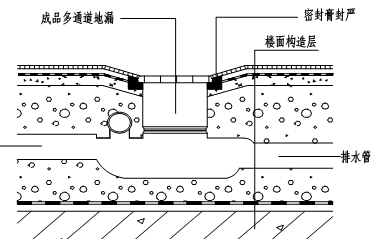
Kitchen floor drain waterproof structure
Six, finished product protection requirements
After the completion of the waterproof layer, the protective layer should be applied immediately to ensure that the coating layer is protected in time. Before the waterproof layer is not inspected, the construction personnel are not allowed to wear leather shoes. Unrelated personnel cannot walk on it, can not stack debris, and are strictly prohibited to walk on the waterproof layer.
Strengthen the education work for construction workers, consciously form a sense of protection of finished products, and take corresponding measures to ensure the performance of the waterproof layer.
Part 2 Roofing (house 1: insulated roof, house 2: non-slip floor tile roof, house 3: planting roof) waterproof project
First, the selection of roofing waterproof engineering materials
Due to long-term exposure, the roof is directly eroded by sunlight, rain and snow. The temperature changes greatly during the harsh winter, and the temperature difference between day and night is large. The roof is prone to deformation and the material is easy to age. Functional boards that are closely related to the living of the roof and other residents, such as roofing, drying, and leisure. It is necessary to improve the reliability and durability of the waterproof seal. Once leaking, it will cause major hidden dangers. The side requires waterproof materials with good aging, certain elongation, weather resistance, high and low temperature resistance.
The figure above shows the reliability of the redundant waterproof seal: Cnr =n!/r!(n-r)!
Output several times = C81 * C81 = 8 * 8 = 64 times
∵Two units form an all-or-door system
If the output is 0 (failed, ie leak), the number of times is only one.
The probability of failure leakage is: P=1/64=0.0156≈ 2%
密封The sealing reliability of the system (probability)=1-P=98%
When selecting roof waterproofing materials, the following requirements should be met:
1. The main material and auxiliary material system are matched to achieve comprehensive fortification and joint sealing, and have reliable water tightness to prevent rain and snow water from leaking into the structure through the roof, penetrating pipeline, deformation joint and gutter.
2, the drainage is rapid, does not cause water accumulation in the waterproof layer.
3, within the durability of the material, under the effect of structural deformation and external factors aging, the waterproof layer is still effective.
4. Meet the requirements of roofing and meet the requirements of urban landscape.
5, the process is simple, no pollution to the environment, the human body, no toxicity.
In summary, when designing roofing waterproofing materials, it is more suitable to use redundant waterproof bonding materials and redundant waterproofing membranes.
Second, roofing waterproof layer design and construction points and practices
a), House 1: Insulated roof level waterproof:
Schematic diagram of waterproof roofing practices:
1.40 thick C20 fine stone reinforcement 砼 2.2 thick YYPE redundant waterproof bonding material +1.2 thick PAWM-3 redundant waterproof coil material 3.50 thick (the thinnest part) ceramsite concrete redundant layer to find 2% slope (waterproof insulation look Slope leveling) 4. Reinforced slab roof panel
2), House 2: Non-slip floor tile roof level waterproof:
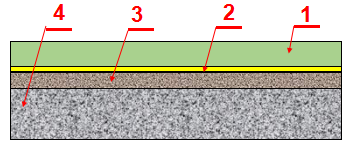
Schematic diagram of waterproofing of anti-slip floor tiles:
1. Non-slip floor tiles 2.2 thick YYPE redundant waterproof bonding material +1.2 thick PAWM-3 redundant waterproof coil material 3.50 thick (the thinnest part) ceramsite concrete redundant layer to find 2% slope (waterproof insulation to find the slope leveling one) 4. Reinforced slab roof panel
c) House 3: Planting roof level waterproof:
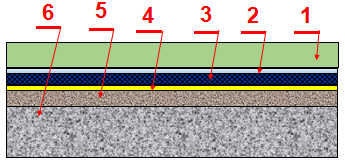
Schematic diagram of planting roof waterproofing:
1. Ceramsite planting soil 2. Geotextile 3.15 thick concave-convex row (storage) water plate + ceramsite water filter layer 4.2 thick YYPE redundant waterproof bonding material +1.2 thick PAWM-3 redundant waterproof coil material 5.50 thick (most Thin section) 2% slope of ceramsite concrete redundant layer (waterproof and heat insulation to find the slope leveling) 6. Reinforced slab roof panel
4), roof waterproof detail node structure:
Third, roof redundant ceramsite concrete insulation, waterproof, slope-finding, leveling integrated construction technology
1. Construction preparation
1) Materials
(1) Cement: No. 325 ordinary cement.
(2) Sand: It is used in general medium sand and requires no impurities.
(3) Ceramsite: clay ceramsite is used. The compressive strength is 2.8 MPa, the bulk density is 525 kg/m3, the apparent density of the particles is 890 kg/m3, the void ratio is 41%, the water absorption is 8.2%, and the specification model is 10-20 mm.
(4) Waterproof admixture: YYM redundant waterproofing agent (type I) is selected. Addition type I: 0.8-1% by weight of cement.
2) Main equipment:
Forced concrete mixer, scale, narrow trolley, flat vibrator, flat boring, clapper, iron roller, small hammer, wire brush, brush, half vat, small bucket, rubber hose, wooden trowel, small kettle, 2 ~3m wooden bars, 5mm and 30mm aperture screens.
3) Working conditions:
The roofing layer has been completed and the concrete slab surface has been cleaned up.
2) Operating process
a, process flow:
Base treatment → Find the high-level gray cake → Ceramic sifting, water boring → Stirring → Laying ceramsite concrete → Maintenance.
Base treatment: The structural base layer is treated before pouring the ceramsite concrete to find the slope layer, the floating slurry and excess concrete are removed, and the above garbage is cleaned with a broom.
Look for the high-grade gray cake: pop the elevation control line on the surrounding daughter wall, make the gray cake according to the slope